日本自動化科技前沿:將人工智能融合到自動駕駛、半導(dǎo)體產(chǎn)業(yè)
【第一對焦:日本】豐田汽車董事長豐田章男宣布:“在硬件領(lǐng)域取得成功的豐田,將變身為融合(AI等)軟件技術(shù)的新企業(yè)。”以AI”明星軍團”為后盾,豐田汽車意在掀起汽車,乃至整個移動世界的變革!富士通綜合產(chǎn)品戰(zhàn)略本部、AI應(yīng)用咨詢部部長山影讓表示:“我們想把AI的創(chuàng)新成果立即傳遞給客戶。”瑞薩電子第二解決方案事業(yè)本部產(chǎn)業(yè)第一事業(yè)部、網(wǎng)絡(luò)解決方案部專家高倉敏說:“AI的優(yōu)點,是能和人一樣,學(xué)習(xí)波形并判定優(yōu)劣。”以往,對良品和不良品的判斷,是交由熟練技工來完成的。但是,技術(shù)人員能夠觀察到的數(shù)據(jù)量有限。而且,由于發(fā)光強度的波形非常復(fù)雜,所以不適合根據(jù)閾值進行管理,且難以實現(xiàn)自動化操作。在這一點上,AI可以像技術(shù)人員一樣從綜合角度判斷優(yōu)劣。實際上,通過運用AI技術(shù),不良品的檢出率提高了6倍。瑞薩半導(dǎo)體制造技術(shù)統(tǒng)括部、流程加工技術(shù)部部長秋元健司表示:“如果能在工序內(nèi)檢測出不良品,將有效避免后工序中無意義的加工,從而大幅降低企業(yè)成本。”
科技生產(chǎn)與生活:日本科技企業(yè)是如何將AI融合到各個領(lǐng)域中的?
科技生產(chǎn)與生活:日本科技企業(yè)是如何將AI融合到各個領(lǐng)域中的?下面我們就來仔細聊聊這個話題。
豐田汽車瞄準的,可不僅僅是自動駕駛,而是將AI應(yīng)用于更廣泛的領(lǐng)域。例如,協(xié)助視力和判斷力下降的老年人駕駛,提升護理用室內(nèi)機器人、汽車的強度,提高燃料電池的效率,降低材料的開發(fā)成本等。在CES現(xiàn)場,豐田汽車甚至還與Preferred Networks等AI研究公司共同展示了具備深度學(xué)習(xí)、自動駕駛能力的汽車演示——8臺自動駕駛車模型互相碰撞后,自動學(xué)習(xí)如何在行駛時避免碰撞。
每輛車上,都載有檢測周圍環(huán)境的傳感器,并以取得的信息為基礎(chǔ),控制油門、剎車、方向盤等。學(xué)習(xí)機制,是在遇到?jīng)_撞時給予處罰,進行強化學(xué)習(xí)。學(xué)習(xí)4小時后,汽車就能避免所有碰撞,順利行駛。該系統(tǒng)的目標,是讓自動駕駛汽車能夠精準識別其他駕駛汽車(包括人工駕駛汽車)可能發(fā)生的沖撞危險,并瞬間避讓。
和視野只關(guān)注前方的人不同,自動駕駛汽車的后方也裝有傳感器,當監(jiān)測到后方有危險時,自動駕駛汽車會毫不猶豫地后退,躲開。豐田汽車董事長豐田章男宣布:“在硬件領(lǐng)域取得成功的豐田,將變身為融合(AI等)軟件技術(shù)的新企業(yè)。”以AI”明星軍團”為后盾,豐田汽車意在掀起汽車,乃至整個移動世界的變革!
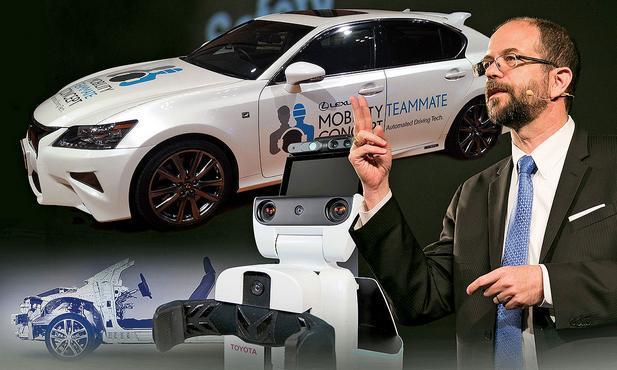
富士通:讓新人,也能做專業(yè)水平的設(shè)計
2015年11月,富士通宣布將本公司的人工智能(AI)技術(shù)系統(tǒng)化,并將其命名為“Zinrai”。名字取自成語“疾風(fēng)迅雷”的日文發(fā)音,意思是麻利、雷厲風(fēng)行。富士通綜合產(chǎn)品戰(zhàn)略本部、AI應(yīng)用咨詢部部長山影讓表示:“我們想把AI的創(chuàng)新成果立即傳遞給客戶。”
通過學(xué)習(xí)以往積攢的設(shè)計數(shù)據(jù),AI能夠精準識別多層基板的層數(shù)。富士通表示,精準估計多層基板的合適層數(shù)很難。因為多層基板很難改變中途的結(jié)構(gòu)設(shè)計——低估層數(shù),可能導(dǎo)致設(shè)計失??;高估層數(shù),可能導(dǎo)致成本上升。也就是說,要在開始詳細設(shè)計之前,就確定好適當?shù)膶訑?shù)。過去,能做到準確估算合適層數(shù)的,只有熟練技工。富士通據(jù)此徹查了整個思考過程:面對龐大的設(shè)計參數(shù),熟練技工的著眼點是什么?調(diào)查結(jié)果顯示,“零件件數(shù)”“引線數(shù)”“網(wǎng)絡(luò)(接線信息)”“基板形狀”等參數(shù)在層數(shù)估算中起了很大作用。
接下來,富士通將這些參數(shù)作為特征量,讓AI學(xué)習(xí)以往的設(shè)計數(shù)據(jù)。通過投入AI應(yīng)用,進入公司第一年的新技工也能達到與熟練技工相同的精準度,估算多層基片的層數(shù)。在運用AI之前,富士通曾經(jīng)研發(fā)過一種算法,只要輸入設(shè)計參數(shù)就能輸出適當?shù)膶訑?shù)。但是,由于設(shè)計參數(shù)的組合過于龐大,在人工開發(fā)問題上存在一定的局限性。富士通研究所制造技術(shù)研究所代理所長澀谷利行表示:“過去,無論怎樣改進算法,機器估算的層數(shù)結(jié)果都無法與人工估算相媲美。但利用AI和大數(shù)據(jù)后,熟練技工感受到了前所未有的壓力。”
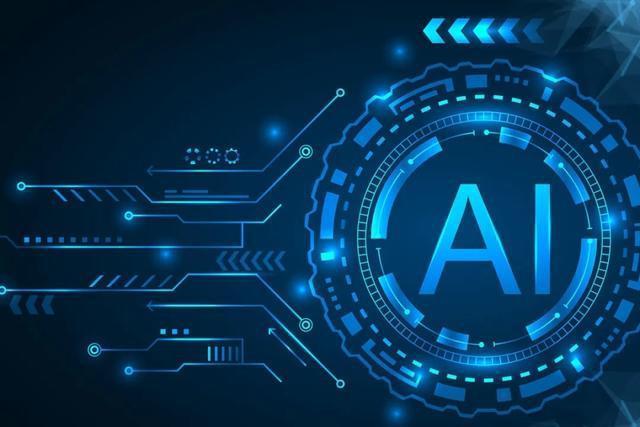
自動編寫和修改程序AI在生產(chǎn)領(lǐng)域的應(yīng)用案例也很多。最常見的,當屬生產(chǎn)線檢查工序等使用的圖像識別程序的制作。例如,在印刷布線基板上安裝零件的線路中,拍攝檢查工序的基板圖像,通過圖像識別程序確認特定的零件是否已被正確安裝。迄今為止,此程序一般是由技術(shù)人員根據(jù)圖像狀態(tài)(亮度、對比度等)和基板設(shè)計制作而成的。但是,一旦圖像狀態(tài)和基板設(shè)計改變,就必須修改程序。這樣一來,如果今后繼續(xù)進行多品種少量生產(chǎn),勢必會出現(xiàn)技術(shù)人員緊缺的情況。因此,現(xiàn)場提出了希望能自動制作和修改程序的要求。
富士通利用通過“遺傳算法”進行學(xué)習(xí)的AI,制作并修改程序。起初,AI的實力只能識別、檢查零件的基本形狀。但現(xiàn)在,AI可以判斷實際安裝的質(zhì)量是否合格。主導(dǎo)此次研究的富士通研究所制造業(yè)技術(shù)研究所特任研究員肥冢哲男表示,AI提取的“形狀的主要模式”的通用性很高,可用于其他種類和形狀的零件。也就是說,即便生產(chǎn)線發(fā)生大規(guī)模的變更,AI也能靈活應(yīng)對。通過運用AI,包含驗證程序在內(nèi)的修改時間,從以往的7天縮減到了8個小時。肥冢哲男說:“晚上學(xué)習(xí)AI后,次日清晨就能制定出新的計劃。”今后,富士通計劃將AI靈活應(yīng)用于機器人操作程序等領(lǐng)域。
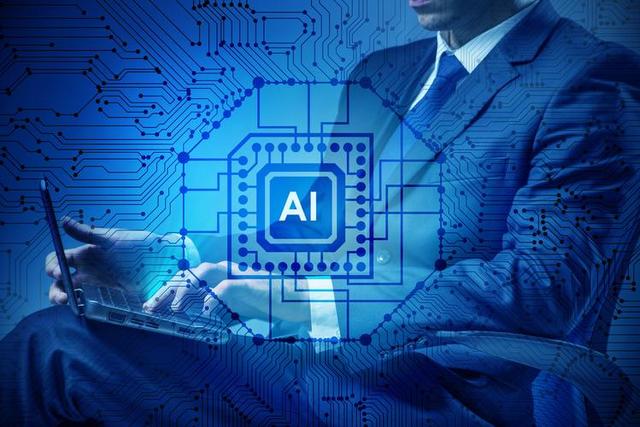
瑞薩電子:讓AI像熟練技工一樣判斷優(yōu)劣
瑞薩電子主要致力于在工廠中應(yīng)用AI。目前,瑞薩電子正在研發(fā)用于FA機器的、組合半導(dǎo)體和AI的解決方案。試驗及應(yīng)用場所,位于其生產(chǎn)子公司瑞薩半導(dǎo)體制造公司的那珂工廠(以下簡稱“瑞薩那珂工廠”)。
成為FA設(shè)備的頭腦原本,瑞薩電子的解決方案依據(jù)的是“邊緣計算”這一概念??偟膩碚f,邊緣計算,是指在網(wǎng)絡(luò)末端(邊緣)設(shè)置的服務(wù)器上,分散處理以大數(shù)據(jù)分析為代表的大規(guī)模計算。一般的大數(shù)據(jù)分析,會將網(wǎng)絡(luò)末端收集到的數(shù)據(jù)集中到云服務(wù)器中,進行集中處理。但是,生產(chǎn)現(xiàn)場對實時性的需求很高,將所有數(shù)據(jù)收集到云服務(wù)器中,或基于分析結(jié)果從云服務(wù)器中控制末端是不現(xiàn)實的。必須使可編程邏輯控制器(PLC)、I/O單元等末端的FA設(shè)備(邊緣裝置)具有高度的數(shù)據(jù)處理功能,從而對大數(shù)據(jù)進行分散性的處理。于是,為塑造邊緣設(shè)備的“頭腦”,瑞薩電子導(dǎo)入了AI。瑞薩電子擁有統(tǒng)一處理CPU、實時操作系統(tǒng)OS和產(chǎn)業(yè)用以太網(wǎng)通信功能的LSI技術(shù)——“R-IN引擎”。
瑞薩電子針對“RIN引擎”開發(fā)出了新的AI模塊,使產(chǎn)業(yè)用LSI適用“R-IN引擎”,并能進行高度的數(shù)據(jù)處理。其目的,是將這種產(chǎn)業(yè)用LSI普及到多個邊緣設(shè)備中。“R-IN引擎”對以往在軟件中實現(xiàn)的實時操作系統(tǒng)OS及產(chǎn)業(yè)用以太網(wǎng)通信功能進行了硬件化,從而提高了CPU的數(shù)據(jù)處理性能。由此產(chǎn)生的余力,被轉(zhuǎn)移到了AI模塊的資源庫,確保了高實時性和高數(shù)據(jù)處理能力。在Al模塊的開發(fā)中,瑞薩電子與CompassIntelligence公司(總部位于東京)展開了合作。在瑞薩那珂工廠,AI被用于判斷半導(dǎo)體生產(chǎn)流程的好壞。具體來說,就是測量等離子蝕刻工序中的等離子發(fā)光強度(電壓),分析繪制在時間軸上的波形,以確定加工質(zhì)量的好壞。等離子體的發(fā)光強度與晶片的加工量密切相關(guān),因此可以從其波形推測出加工質(zhì)量。
比較實際測量值(輸入波形)與學(xué)習(xí)后的AI得出的預(yù)測值(再生波形),對兩者之間的差的累積值(錯誤波形)進行閾值管理。想讓AI判斷優(yōu)劣,必須先輸入大量的良品和不良品數(shù)據(jù)。AI將基于該數(shù)據(jù),學(xué)習(xí)良品模式。向完成學(xué)業(yè)的AI輸入實際測量的數(shù)據(jù)時,AI會基于實際輸入值和良品模式,模仿該波形輸出另一波形。如果是良品,那么輸入波形與再生波形基本一致。如果是不良品,則會產(chǎn)生偏差。AI通過對兩者之間的差的累積值進行閾值管理,判定優(yōu)劣。
擔(dān)負繁雜工作以上案例,還充分利用了CPU處理性能高的“R-IN引擎”的特點。在一般的FA設(shè)備中,對等離子體的發(fā)光強度進行取樣是以1秒為單位的。而采用“RIN引擎”的FA設(shè)備可進行50毫秒(1毫秒=0.001秒)的采樣,大大提高了判定結(jié)果的精度。這樣的精度,不僅可以用于判定產(chǎn)品優(yōu)劣,還可以用于預(yù)先維護生產(chǎn)設(shè)備等方面。瑞薩半導(dǎo)體制造執(zhí)行董事井上修一說:“我現(xiàn)在覺得,繁雜的業(yè)務(wù)已經(jīng)可以交給AI去處理了。”
微信聯(lián)盟:自動化科技微信群、人工智能微信群、豐田微信群、富士通微信群、瑞薩電子微信群、解決方案微信群、自動駕駛微信群、半導(dǎo)體產(chǎn)業(yè)微信群、汽車產(chǎn)業(yè)微信群、制造業(yè)微信群、模式識別微信群、生產(chǎn)線自動化微信群、工廠自動化微信群,各細分行業(yè)微信群:點擊這里進入。
鴻達安視:水文水利在線監(jiān)測儀器、智慧農(nóng)業(yè)在線監(jiān)測儀器 查看各品牌在細分領(lǐng)域的定位宣傳語


評論排行