科技新進展:鞍鋼智慧高爐大數(shù)據(jù)可視化平臺建設與示范應用
科技新進展:鞍鋼智慧高爐大數(shù)據(jù)可視化平臺建設與示范應用
一、研究的背景與問題
《中國制造2025發(fā)展規(guī)劃》明確要求傳統(tǒng)的制造業(yè)要向數(shù)字化、網(wǎng)絡化、智能化、綠色化發(fā)展,支持傳統(tǒng)產(chǎn)業(yè)優(yōu)化升級,尤其是鋼鐵行業(yè)依靠信息化、智能化技術,把傳統(tǒng)的鋼鐵企業(yè)轉(zhuǎn)型成智能制造企業(yè)。在鋼鐵工業(yè)中高爐的生產(chǎn)成本、能源消耗、CO2排放量均占70%以上,是制約鋼鐵行業(yè)競爭力的瓶頸。由于高爐及其附屬工序設備工藝多樣復雜性、生產(chǎn)過程不確定性,以及所有變化過程均發(fā)生在大封閉性的高爐內(nèi)部,難以直接檢測,屬于典型“黑箱”問題,到目前為止,高爐操作依然是以高爐操作者經(jīng)驗為主,難以做到高爐長期高效低耗和爐況穩(wěn)定順行。鞍鋼高爐眾多,高爐群也難以被統(tǒng)一管理。因此迫切需要建設資源共享、優(yōu)勢互補、高效協(xié)同的大數(shù)據(jù)集約化與可視化管控平臺,以提升高爐群整體協(xié)同效率。
鞍鋼高爐及其附屬工序之間多工序和各高爐之間在一體化管理方面存在的一些難題:一是缺少統(tǒng)一智能化管理平臺,爐況、生產(chǎn)信息零散不集中,分散獨立,數(shù)據(jù)共享和分析挖掘不夠。二是協(xié)同響應滯后,由于時空阻隔,協(xié)同信息、需求信息滯后;部分信息經(jīng)層層過濾,準確性、及時性受限。三是缺少統(tǒng)一的評價體系,由于高爐群工藝裝備、原燃料、操作模式的差異,指標先進性、運行狀態(tài)評價體系不一致。四是語言、標準尚未完全統(tǒng)一,一些工藝參數(shù)名稱、計算方法、異常爐況的判別、操作應對標準、各高爐操作手法與偏好不一致。
基于以上背景與需要,鞍鋼從2007年開始,逐漸補充和完善煉鐵產(chǎn)線上檢測工業(yè)傳感器的同時,積極同北京科技大學合作,從高爐冶煉機理和傳輸原理層面進行數(shù)學建模以揭示高爐“黑箱”內(nèi)的反應及狀態(tài),為鞍鋼兩化融合實現(xiàn)智能化煉鐵打下基礎。近年來,通過大數(shù)據(jù)挖掘技術運用,開發(fā)了“鞍鋼智慧高爐大數(shù)據(jù)可視化管控平臺,實現(xiàn)了高爐群及附屬工序數(shù)據(jù)資源共享、優(yōu)勢互補、高效協(xié)同的統(tǒng)一管理,并打通傳統(tǒng)各級信息化系統(tǒng)之間的數(shù)據(jù)孤島,完成高爐煉鐵從智能單元到智能平臺的升級。此外以高爐大數(shù)據(jù)平臺為基礎,從煉鐵機理層面定制開發(fā)“一爐一策”高爐數(shù)學模型,開發(fā)高爐爐缸侵蝕狀態(tài)3D可視化監(jiān)控模型,建立基于數(shù)據(jù)挖掘高爐群爐況評價體系,對不同爐型高爐冶煉過程實施統(tǒng)籌智能管理,使得鞍鋼煉鐵工序全流程得到轉(zhuǎn)型升級,極大提升高爐生產(chǎn)、技術與管理的數(shù)字化、科學化、智能化水平,完美實現(xiàn)高爐冶煉過程從“黑盒”向“白盒”的重要突破。
二、解決問題的思路與技術方案
根據(jù)鞍鋼高爐的設計、生產(chǎn)和操作特點,基于冶金基礎理論與人工智能前沿技術,定制開發(fā)高爐數(shù)學模型,實現(xiàn)高爐的高效生產(chǎn),提升高爐生產(chǎn)、技術與管理的整體數(shù)字化、科學化、智能化水平,同步實現(xiàn)高爐煉鐵的安全長壽、低耗高效、清潔生產(chǎn),實現(xiàn)高爐冶煉從“黑盒”向“白盒”的重要突破。總體思路如圖1所示:
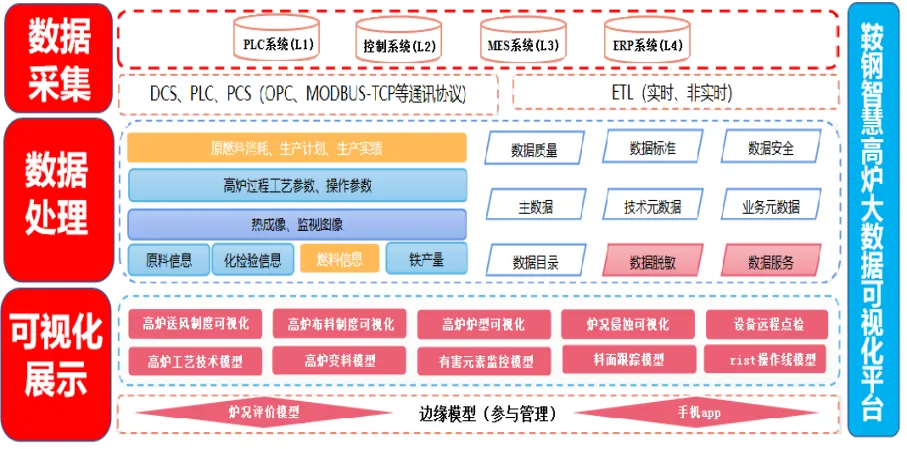
圖1 項目研究總體思路圖
1、建立高爐群生產(chǎn)大數(shù)據(jù)平臺
建立高爐生產(chǎn)過程操作參數(shù)數(shù)據(jù)倉庫、完成不同數(shù)據(jù)庫的各種接口和數(shù)據(jù)統(tǒng)一表示,用于支撐外部數(shù)據(jù)采集、內(nèi)部數(shù)據(jù)整合;利用控制系統(tǒng)所提供的OPC服務器功能,編寫OPC客戶端程序,實現(xiàn)從基礎自動化系統(tǒng)中讀取生產(chǎn)過程實時數(shù)據(jù)。高爐生產(chǎn)過程信息化、智能化平臺建設項目結合物聯(lián)網(wǎng)建設,數(shù)據(jù)采集、通訊、數(shù)據(jù)清洗、數(shù)據(jù)預處理、數(shù)據(jù)分類、存儲等建立數(shù)據(jù)平臺和大數(shù)據(jù)處理中心,為基于數(shù)據(jù)平臺開發(fā)工藝機理和統(tǒng)計數(shù)學模型、大數(shù)據(jù)分析與挖掘、機器學習、專家系統(tǒng)等提供保障,同時滿足廠長、廠調(diào)度、公司調(diào)度及其他管理及科研部門的需求。
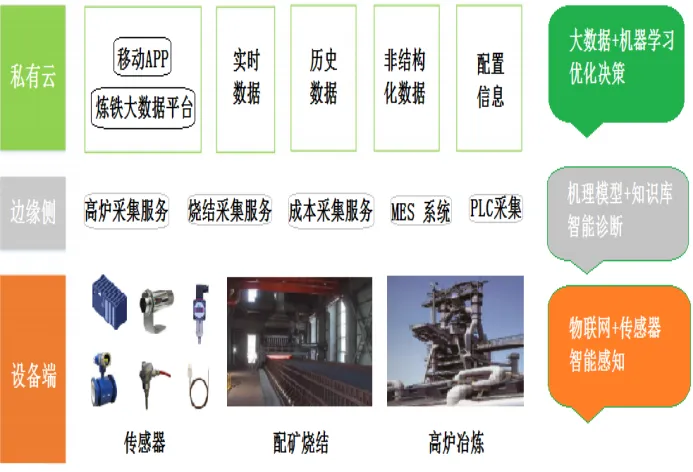
圖2 鞍鋼高爐大數(shù)據(jù)平臺構架
2、基于高爐大數(shù)據(jù)平臺的高爐“一爐一策”可視化平臺開發(fā)
高爐機理建模與數(shù)字化仿真系統(tǒng)融合機理的全高爐綜合數(shù)學模型,實現(xiàn)全高爐仿真和工作狀態(tài)精確解析,提供高爐爐況預測結果和匹配操作的推送、完成高爐操作變更影響因素的推送、完成高爐運行趨勢分析結果的推送和歷史數(shù)據(jù)溯源結果的推送。
3、高爐爐缸爐底多維冗余侵蝕計算模型和結構安全指標預警機制評估系統(tǒng)
以鞍鋼不同爐容高爐爐缸的破損調(diào)查為基礎,綜合檢測不同種類炭磚;并建立炭磚合理的評價制度;利用高爐破損調(diào)查結果不斷深入的校正計算模型。
4、基于數(shù)據(jù)挖掘的高爐健康狀態(tài)的評價體系
挖掘影響高爐生產(chǎn)和操作的主因、隱因以及高爐操作關聯(lián),研究高爐冶煉參數(shù)的關聯(lián)分析、高爐操作規(guī)則的關聯(lián)分析和歷史數(shù)據(jù)溯源。高爐大數(shù)據(jù)全流程挖掘與云計算。將歷史數(shù)據(jù)與當前操作關聯(lián),實現(xiàn)高爐生產(chǎn)過程多種操作參數(shù)優(yōu)化,推算最佳高爐工藝路線。
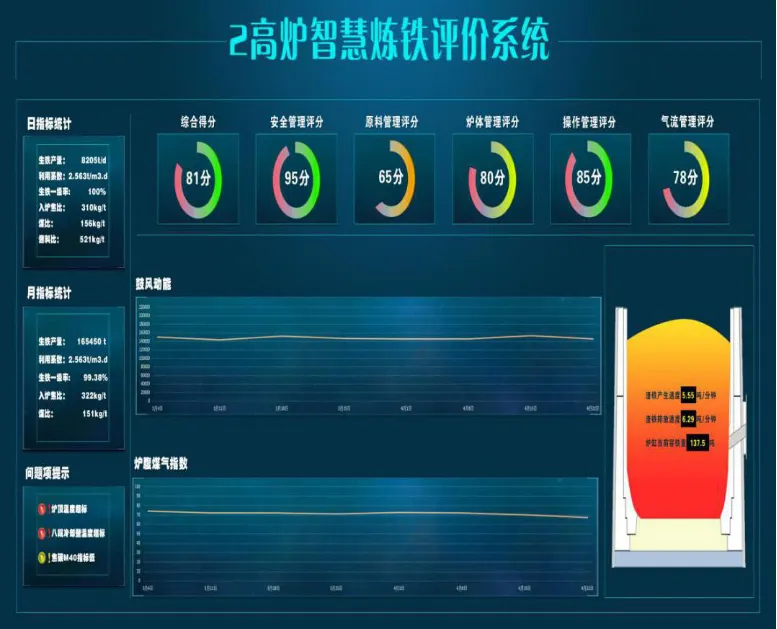
圖3 關鍵參數(shù)預警診斷系統(tǒng)
三、主要創(chuàng)新性成果
1、建立鞍鋼高爐群大數(shù)據(jù)平臺
基于工業(yè)物聯(lián)網(wǎng)、云存儲、云計算等技術完成高爐及附屬工序、MES系統(tǒng)、ERP系統(tǒng)數(shù)據(jù)整合,打破信息孤島,建立以高爐群為核心的大數(shù)據(jù)集約化管控平臺,實現(xiàn)高爐生產(chǎn)狀態(tài)的全息再現(xiàn)。
2、建立高爐“一爐一策”可視化平臺
在高爐大數(shù)據(jù)云平臺交互基礎上開發(fā)高爐生產(chǎn)工藝模型和移動終端APP,對高爐冶煉全過程進行全方位、實時可視化監(jiān)控。實現(xiàn)高爐生產(chǎn)全流程物質(zhì)流與能量流信息化管控、高爐操作爐型和冷卻壁安全監(jiān)測與預警、高爐裝料及布料過程智能仿真、爐頂料面與煤氣流分布及風口回旋區(qū)的三維可視化監(jiān)控。
3、鞍鋼高爐爐缸侵蝕狀態(tài)高精度預判及三維可視化監(jiān)控模型開發(fā)與應用
基于高爐破損調(diào)查炭磚特征和性能指標檢驗結果,修訂炭磚搗料的導熱系數(shù),建立高精度高爐炭磚殘厚計算數(shù)學模型,并利用計算機圖形學技術對數(shù)據(jù)結果作處理,實現(xiàn)了爐缸內(nèi)襯侵蝕程度的精準判斷和侵蝕形貌的循環(huán)動態(tài)展示。
4、建立基于數(shù)據(jù)挖掘高爐群爐況評價體系
對高爐冶煉全流程進行數(shù)據(jù)挖掘與深度解析,建立高爐冶煉參數(shù)與高爐經(jīng)濟技術指標的關聯(lián)性評價體系,實時對高爐的健康狀況進行打分并做出智能診斷和優(yōu)化建議。
四、應用情況與效果
本項目成果已在鞍鋼本部煉鐵總廠2號、3號高爐(3200m3)、5號高爐(2580m3)和鲅魚圈分公司煉鐵部1號、2號高爐(4038m3)實施應用,同時煉鐵總廠1號、2號、3號、10號高爐(3200m3)4號、5號高爐(2580m3)初步實現(xiàn)集控功能,從生產(chǎn)、操作、技術、管理、培訓等全方位提升鞍鋼煉鐵的數(shù)字化、科學化、智能化、標準化水平,取得如下效果:
?。?)將遙感測溫、三維激光雷達、熱成像等新技術應用于傳統(tǒng)煉鐵工業(yè)傳感及物聯(lián)網(wǎng)開發(fā),實現(xiàn)對高爐群、燒結機、球團機等煉鐵核心設備及大數(shù)據(jù)的在線監(jiān)測,達到了減少較危險的點檢和爐前工作對人的依賴,降低了安全事故發(fā)生率;
?。?)建立基于工藝機理、大數(shù)據(jù)、機器學習、互聯(lián)網(wǎng)+的配礦、燒結、球團、高爐智能控制系統(tǒng)的煉鐵大數(shù)據(jù)智能可視化與集控平臺實現(xiàn)鞍鋼高爐群各產(chǎn)線煉鐵數(shù)據(jù)互聯(lián)互通和復雜的鐵前各工序高效協(xié)同,高爐操作人員勞動生產(chǎn)率提高44%;
(3)建立高爐冶煉過程可視化云平臺及移動終端APP高爐診斷模式,初步建立“煉鐵移動工廠”,冶煉取得了從“黑盒”向“白盒”的重要突破,煉鐵操作和爐況分析由原先依靠人工經(jīng)驗和主觀判斷為主轉(zhuǎn)變?yōu)橐揽繑?shù)據(jù)為主,項目實施后,本部煉鐵總廠2、3、5號高爐和鲅魚圈煉鐵部1、2號高爐在入爐品位較低、大量使用外購焦和濕熄焦條件下,5座高爐利用系數(shù)平均提升0.487t/(m3?d),指標達到國內(nèi)先進水平。
截止目前,本成果授權發(fā)明專利14件,登記軟件著作權4項,發(fā)表高水平研究論文28篇。
信息來源:鞍鋼股份有限公司
我要收藏
點個贊吧
轉(zhuǎn)發(fā)分享
咨詢詳情:如需咨詢文中涉及的相關產(chǎn)品或解決方案詳情,請加微信:ZiDongHuaX 。
微信聯(lián)盟:智慧高爐微信群、智能制造微信群、鋼鐵工業(yè)微信群、人工智能微信群,各細分行業(yè)微信群:點擊這里進入。
鴻達安視:水文水利在線監(jiān)測儀器、智慧農(nóng)業(yè)在線監(jiān)測儀器 查看各品牌在細分領域的定位宣傳語
微信聯(lián)盟:智慧高爐微信群、智能制造微信群、鋼鐵工業(yè)微信群、人工智能微信群,各細分行業(yè)微信群:點擊這里進入。
鴻達安視:水文水利在線監(jiān)測儀器、智慧農(nóng)業(yè)在線監(jiān)測儀器 查看各品牌在細分領域的定位宣傳語


評論排行